As a small business owner, you are constantly striving to push past obstacles and propel your business forward. In spite of that, it is still easy to get stuck in a rut, unsure of the next steps to take. Fortunately, there are proven strategies and methodologies that can help you break free from this cycle of stagnation and unlock your business’s full potential.
Understanding Waste
In the fast-paced world of business, every moment counts, and inefficiencies can drain both time and resources. Yet, many small business owners overlook the hidden costs of waste within their operations. According to Lean Six Sigma principles, ten types of waste can plague businesses, from excessive transportation and inventory to over-processing and defects. These inefficiencies not only drain your resources but also hinder your ability to scale and thrive.
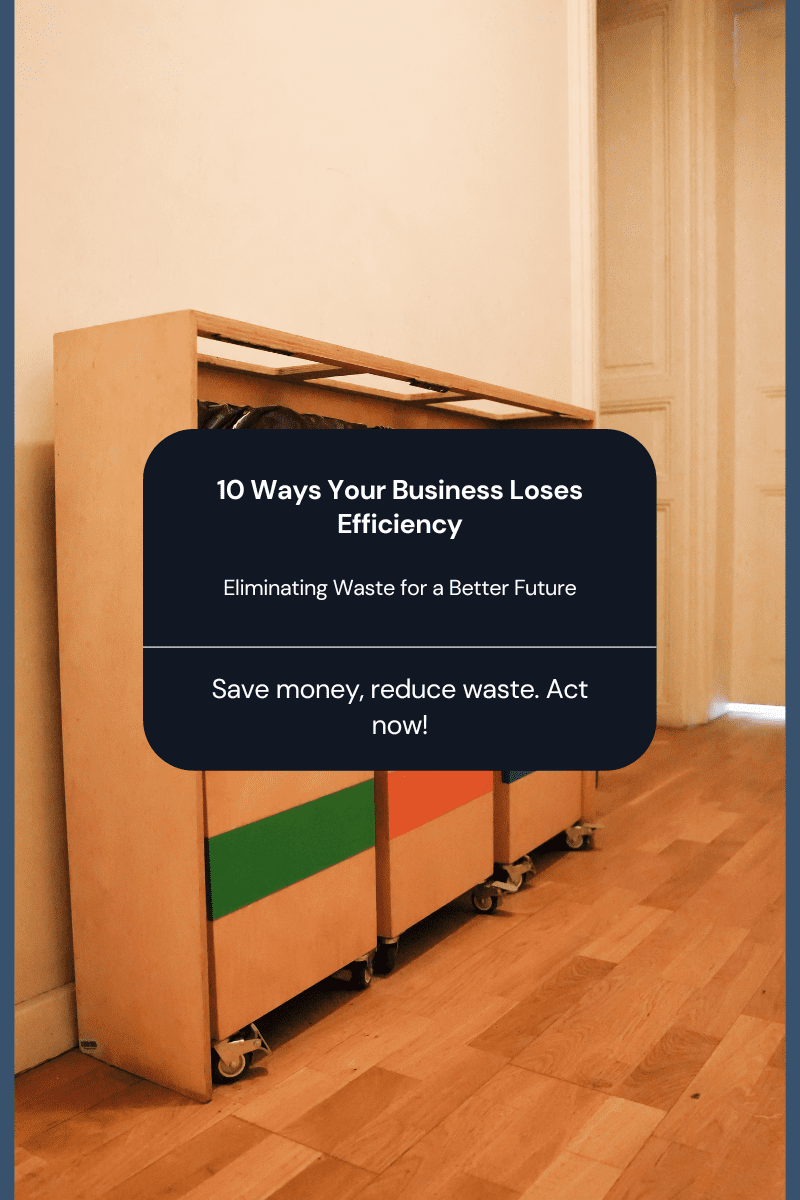
10 Types of Waste
When we talk about eliminating waste from an organization, we focus on ten main areas (we’ve talked about seven more common ones already). Think through your systems and processes, where can you improve?
- Transportation: Excessive transportation adds unnecessary costs, increases the risk of damage to products, and can lead to delays in delivery, impacting customer satisfaction and potentially increasing lead times.
- Inventory: Excess inventory ties up capital, incurs storage costs, and increases the risk of obsolescence. It can also mask underlying problems in the production process, such as inefficiencies or defects.
- Motion: Unnecessary motion can lead to inefficiencies, fatigue, and even workplace injuries. It reduces productivity and can contribute to errors or accidents, impacting quality and safety.
- Waiting: Idle time due to waiting wastes resources and decreases productivity. It increases lead times and can result in missed deadlines or customer dissatisfaction.
- Overproduction: Producing more than what is immediately required by customers leads to excess inventory, increased storage costs, and potential waste of resources. It also increases the risk of obsolescence and can strain cash flow.
- Overprocessing: Performing unnecessary or overly complex tasks consumes resources without adding value. It increases production costs, extends lead times, and can result in higher prices for customers without corresponding benefits.
- Defects: Defects result in rework, scrap, or customer returns, increasing costs and reducing profitability. They also damage the reputation of the business, leading to decreased customer satisfaction and potential loss of future business.
- Skills: Underutilization of employees’ skills leads to decreased morale, engagement, and productivity. It also inhibits innovation and improvement, as valuable insights and ideas from employees go untapped.
- Unused creativity: Failing to leverage employees’ creativity and problem-solving abilities results in missed opportunities for process improvement and innovation. It can lead to stagnation, reduced competitiveness, and ultimately, decreased market share.
- Excess processing: Additional processing consumes resources without adding value, increasing costs and lead times. It can also introduce opportunities for errors or defects, further impacting quality and customer satisfaction.
Strategic Action Items
Ready to take the next step? Eliminating waste doesn’t have to be overwhelming! Here are three things you can do.
- Mindset Shift: Embrace a proactive mindset by recognizing that inefficiencies are not inevitable but rather opportunities for improvement. Challenge yourself to think critically about your business processes and identify areas for optimization.
- Systemization and Process Improvement: Take a deep dive into your operations to identify bottlenecks, redundancies, and other sources of waste. Implement Lean Six Sigma principles to streamline your processes, improve efficiency, and maximize productivity.
- Invest in Professional Support: Recognize when you need outside expertise to address complex challenges effectively. Our team of certified Lean Six Sigma professionals is here to guide you every step of the way, offering personalized solutions tailored to your unique business needs.
Take the Next Step
Are you ready to take your business to the next level? Schedule an appointment with one of our specialists to explore how our unique approach can help you overcome challenges, unlock opportunities, and achieve the growth you deserve. Let’s work together to transform your business — so you can focus on working on it, not just in it. You don’t have to spend time eliminating waste by yourself. Trust our proven process!